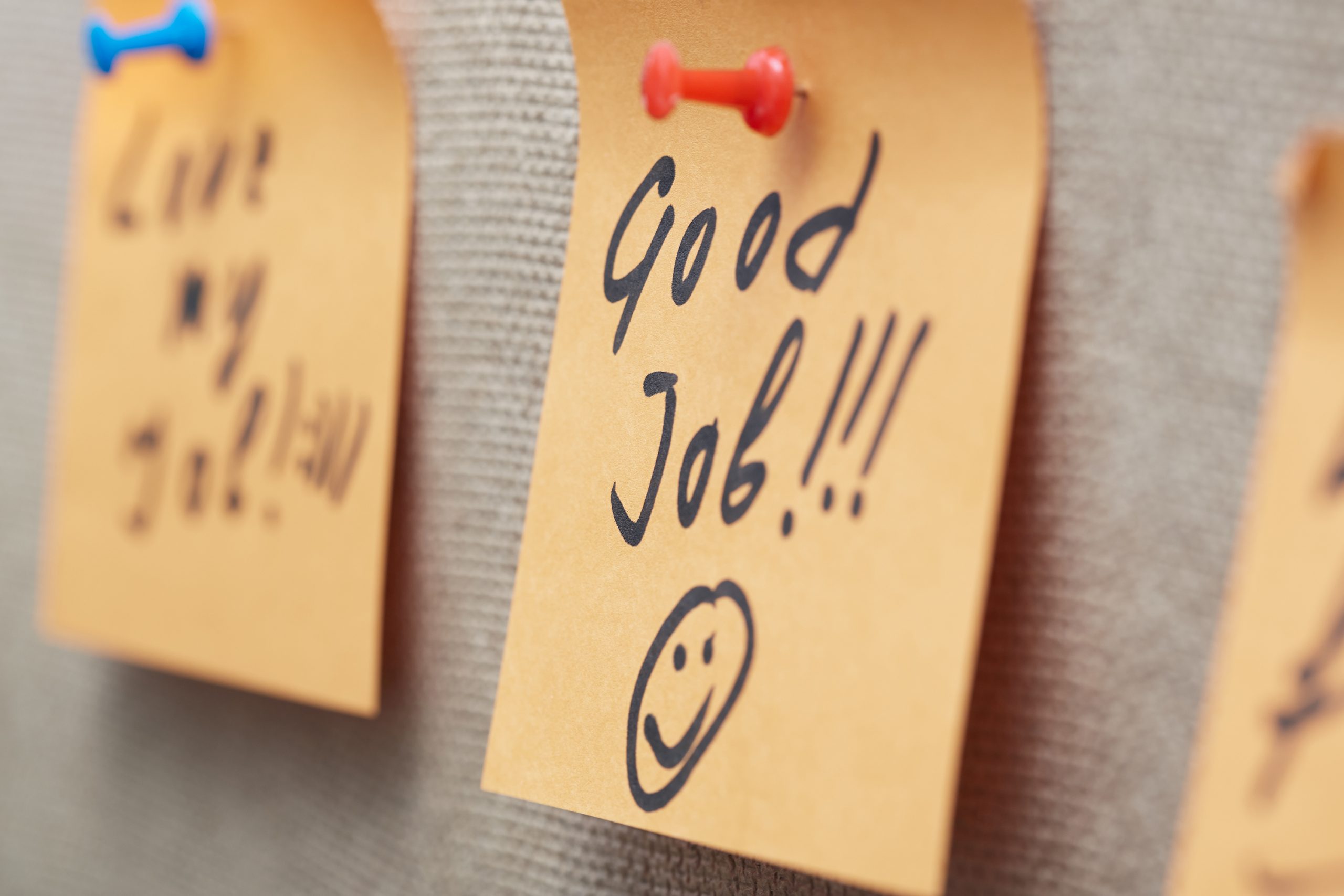
What’s so good about working safely? Investigating when things go right
Psychologists will tell you that, as humans, we have a natural bias to focus on the negative. We might receive ten compliments on a presentation or report but it’s the one slightly negative comment that we dwell on.
Nick Wharton looks at why the traditional approach to safety – measuring failures, lost time injuries and non-compliance, means that we may be missing a trick. He believes that there is just as much to learn from what goes well in safety and that we should always pay attention to the ‘non-accidents’ and pockets of excellence.
Following an accident or incident on site, we undoubtedly gather the team together and ask the question “What went wrong?” We take the opportunity to learn from our mistakes – a basic principle in making sure the incident is not repeated.
So, why don’t we do this when things go right? There is so much we can learn from projects that run smoothly, without mishap or injury, so we can continue to keep people safe.
This is the thinking behind Professor Erik Hollnagel’s simple but valid theory of ‘Safety-I and Safety-II’ He explains that accident investigation and risk assessment models traditionally focus on what goes wrong (Safety-I). Performance is measured through a lack of failure and generally trying to reduce the frequency with which bad things happen.
Safety is measured by counting the number of cases where it fails rather than by the number of cases where it succeeds
A more positive approach (Safety-II) is to take the time to learn when things go well. If we can really understand why nobody was hurt or why the task was successful, we can make sure that we continue to repeat this performance in future.
In simple terms, Safety-I focuses on minimising the bad, while Safety-II focuses on maximising the good.
Creeping complacency?
As organisations continue to improve their H&S performance – as most do, we are seeing fewer and fewer accidents, incidents and injuries. This is great news and thanks, in no small part, to the hard work and dedication of local managers supported by H&S professionals.
Fantastic as it is to see less people being harmed at work, there is a potential that we run out of opportunities to learn vital lessons to sustain the improvement. There is also a possibility that a degree of complacency could creep in with the workforce taking it for granted that injuries do not occur.
Both these situations can be prevented by taking the time to investigate success with as much careful scrutiny as if it were an accident that we were following up.
Really understanding why a task went well or why nobody was adversely affected will help to ensure that it wasn’t just good luck.
By identifying and explaining how and why success was achieved, we can demonstrate to the whole team that it is only through positive action that everyone stays safe. A passive approach that just assumes all will continue to be okay will not guarantee that everyone continues to go home safe and well.
Why not take a look at what’s good?
Start by trying this approach with a discreet project that runs smoothly without incident or injury. Get a team together in just the same way as you would if the outcome had not been so good.
“Why did nobody get hurt?”
“Because everyone knew what they were doing.”
“How come?”
“They had all received training and had been briefed clearly.”
“Tell me about the briefing.”
“The Supervisors were provided with clear notes; they were given time to get their teams together; they talked them through the job, step by step and encouraged anyone with any questions or concerns to speak up. Everyone had a chance to chip in and share previous experiences.”
“Sounds great. Anything else?”
‘The job was well planned beforehand, involving the people who really understand the realities, so adequate time and resources were allocated.”
Clearly this is no different to the sort of detailed investigation that we would conduct if something had gone wrong.
The lessons are there to be identified and shared with others so as to increase the likelihood of future success. In time, it should become natural for Team Leaders at every level to be regularly reviewing every task, project or shift, to identify and therefore maximise all the good things that happen.
Imagine the positive shift in mindset this approach will breed.
About Nick Wharton
Lead Consultant
My role is to work with clients from many industries, in many countries, helping them to achieve the culture change they seek. I draw on my years of experience in enforcement, as an HSE Manager in industry and for many years as a Director of Tribe and its predecessor JOMC. During this time, I managed our excellent group of experienced and knowledgeable consultants, as well as overseeing the development of the many and varied new tools and approaches we use to help in getting the safety message across and achieving Culture Change.