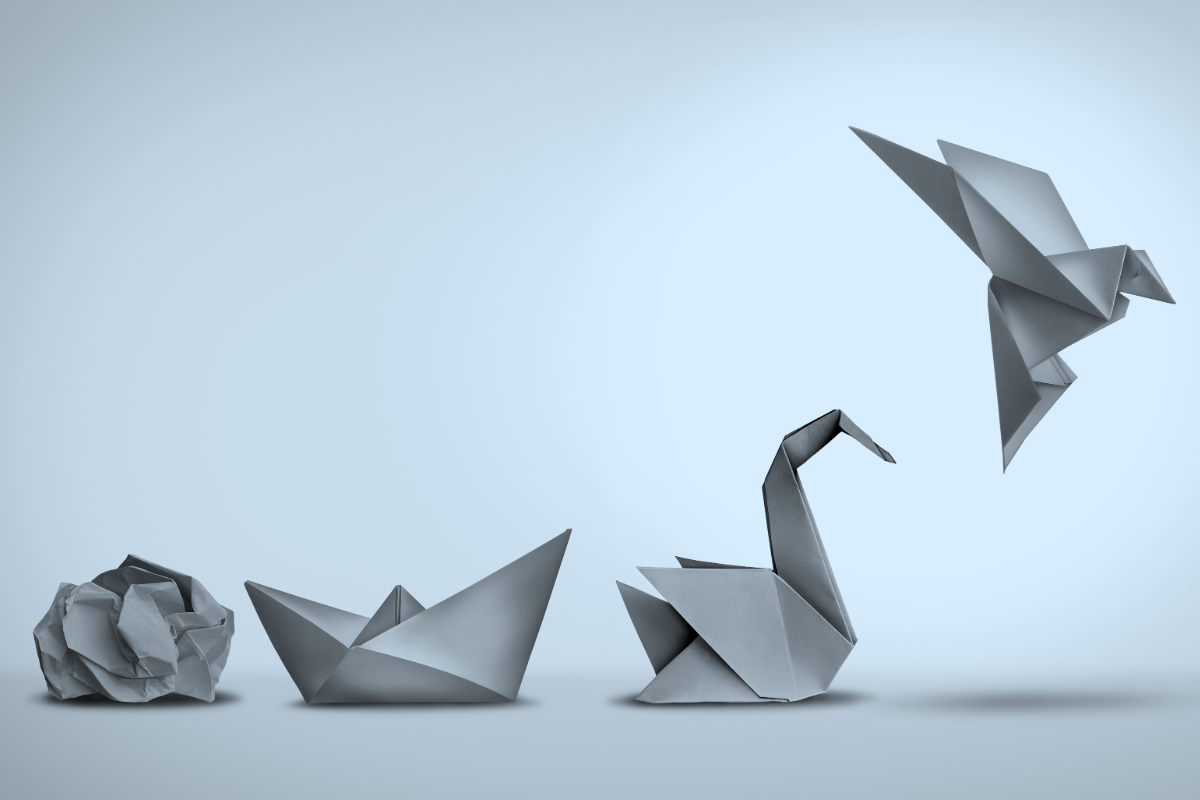
3M: How to Create a Lasting Culture that Sticks
Most safety culture change programmes start with a buzz of excitement and high expectations. But as time goes by, loss of momentum and dwindling enthusiasm risks your programme going stale.
“During our programme’s honeymoon we expected things would change, but it wasn’t that immediate. Then we had our ‘eureka moment’ – we realised that lasting culture change needs periods of reinvigoration.”
Adrian Hughes and Martyn Harvey of 3M Occupational Health & Safety Division have nurtured an award-winning safety culture at their Aycliffe manufacturing plant where they’ve achieved sustained periods without an LTA.
“It takes hard work at the start but as our programme matured safety’s become a core value… it’s non-negotiable and it’s what Aycliffe’s known for.”
Ask your staff what they think
Early on, 3M acknowledged that their plan for a safer culture needed refreshing regularly. And the secret to their success lies with plenty of involvement from staff. Every three years they survey their workforce to capture values and beliefs of their shop floor staff:
“Questionnaires and interviews are an invaluable tool. They let you measure the changes and improvements you make so it’s more visible.”
Yet Adrian Hughes, EHS Manager at 3M’s Aycliffe site, argues that it’s not the evaluation tools you use that are unique, it’s more the approach you take. Engaging with staff, acting on the results and then measuring your success gives you a structure to follow. It guides you in the right direction by providing feedback along the way, as Adrian points out:
“If your organisation isn’t using similar vehicles to measure improvement you’re missing a trick. You can’t just sit there with your fingers crossed hoping for results.”
Inspire people to buy-in
For any approach to be effective you need everyone behind it. Martyn Harvey, EHS Coordinator also at 3M’s Aycliffe site, suggests that sustained culture change success needs inspiration, involvement and awareness:
“We run workshops with guest speakers, typically workplace accident victims… To take that step and have an individual sat a few yards away from you talking about a real event, it becomes real… what went wrong and how their life has never been the same again.”
The tipping point
Lasting culture change takes hard work to begin with. But as your programme embeds itself, leaders gradually take ownership and spread your safety message for you. So your responsibilities shift to training the trainers, something 3M did with support from JOMC:
“We put great emphasis on good quality training and refreshing people… we remind them about the balance between knowing how to spot the consequences of a job going wrong and when to nod your head and say ‘good job, keep it up’.”
Wrap it up
Adrian and Martyn agree; your safety culture change programme is a continual journey. And periodic reinvigoration is critical to remind your staff about their individual responsibilities as well as the fundamental reasons behind why your programme exists at all.
“It’s about making sure everything stays fresh, credible and balanced so people buy into what you’re trying to do. And you can’t present the same thing twice, it’s the same message, but you have to wrap it up differently each time.”
Echoing Adrian, Martyn underlines that message: “nothing you do is worth getting hurt for. We want our staff to come in healthy and go home healthy.”